A Sneak Peek at our Core i9-9900K Sample
by Ian Cutress on October 11, 2018 9:55 AM EST- Posted in
- CPUs
- Intel
- Core 9th Gen
- i9-9900K
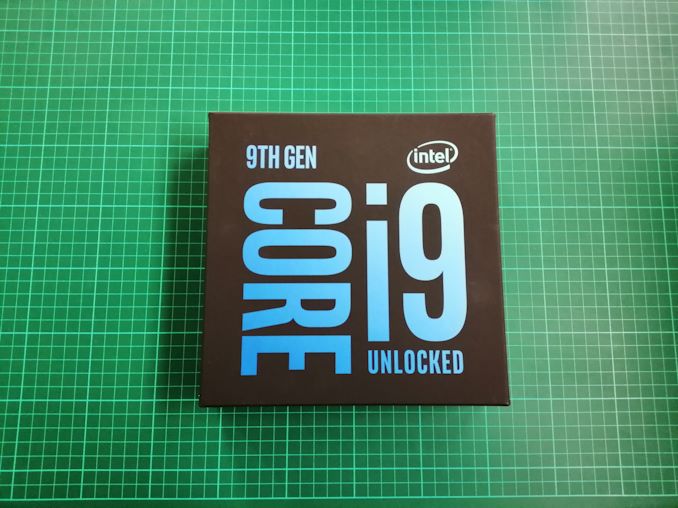
Before I had even landed back home from Intel's 9th Gen announcement event in New York, the Core i9-9900K sample from Intel had arrived. We still have some time before we can publish our results, but we can still take a look at how Intel packaged it up for us. A fair warning: we didn't get the flashy d12 case shown on stage.
This One Doesn't Roll
Shown on stage at Intel's event was a brand new flashy box design in the form of a dodecahedron. It looks exactly like a 12-sided die, similar to those used in dice-based games such as D&D. Its full size isn't much more than the size of one's hand.
Here is Intel's Anand Srivatsa holding the flashy design on stage. Roll for initiative, I guess?
Intel 9th Gen Core | |||||||||
AnandTech | Cores | TDP | Freq | L3 | L3 Per Core |
DRAM DDR4 |
iGPU | iGPU Turbo |
|
Core i9-9900K | $488 | 8 / 16 | 95 W | 3.6 / 5.0 | 16 MB | 2.0 MB | 2666 | GT2 | 1200 |
Core i7-9700K | $374 | 8 / 8 | 95 W | 3.6 / 4.9 | 12 MB | 1.5 MB | 2666 | GT2 | 1200 |
Core i5-9600K | $262 | 6 / 6 | 95 W | 3.7 / 4.6 | 9 MB | 1.5 MB | 2666 | GT2 | 1150 |
Intel is releasing three processors next week, although Intel is only sampling the Core i9-9900K.
The Press Kit
Instead of the dodecahedron, Intel plumped for a customized box. Inside, we were greated with our name.
Intel's big thing for the Core i9 and the 9th generation parts is the motto 'performance unleashed', by moving up to eight cores on the Core i9 series. All of this inside is cardboard, with the processor underneath.
Intel has supplied the press with engineering samples, that show off the S-Spec name of QQPP, and the base frequency of 3.60 GHz.
There's not much else to say. Intel is sampling the Core i9-9900K only, and motherboard vendors have started shipping out samples. We have reviews of the motherboards soon, and our 9th gen review will be going live on the embargo day, October 19th.
Edit: Peek for Peak in title. Too many peeks.
28 Comments
View All Comments
imaheadcase - Thursday, October 11, 2018 - link
I'm thinking out loud here, but does anyone else thing CPU are going to venture away from square designs. I mean i read a long time ago that humans just do that so things fit into other things, but its more efficient to make hardware differently...just standards make it so they can't do own thing.A5 - Thursday, October 11, 2018 - link
All of the wafer tools are designed for rectangular dies, so until that changes it probably doesn't make any sense to move away from rectangular/square packaging.PGFan - Thursday, October 11, 2018 - link
The squarish designs also maximize the surface area for pins. A long time ago, chips that used DIP were rectangular, but were also limited on the number of pins because of the shape (and the pins were wide mounted and not bottom-mounted). Think 8080-80286. My last DIP-based CPU, if I recall correctly, was a V20 replacement for a 8088.sing_electric - Thursday, October 11, 2018 - link
In theory, if you wanted to maximize space while minimizing surface area for a chip (say, on a motherboard), round would be best. (It also doesn't hurt that fans have to be round, and every desktop processor is dependent on active cooling, typically fans.)However, two main issues: In the end, the question is how many chips you can fit on a wafer, since that's the biggest driver of cost. Putting a bunch of circles next to each other would result in a LOT of dead space. There might be some kind of polygonal array that'd theoretically minimize wasted area on the outside, but it would be dependent on chip and wafer size.
Given some chips have MUCH bigger dies but fit into the same package (e.g. a quad core i5 and an 8 core i9 use the same socket), it'd be very hard to plan that out.
Second, knowing how to orient a square processor is easy: Just mark a corner. You'd have to get the rotation of a round processor EXACTLY right, which would probably be way trickier (there might be some fancy way of mounting a round processor, like how lenses are "twisted" in to the socket, at which point the pins line up, except I don't think that'd scale well to over 1,000 tiny pins - I think mechanical breakage would be a significant concern).
Oh, and also: As it stands, motherboard makers don't seem to have to remove a ton of features to accommodate a larger processor, for example, how an ATX Ryzen and Threadripper motherboard might have the same # of PCI-X, RAM, SATA, etc. slots.
willis936 - Thursday, October 11, 2018 - link
Hexagon is 2D closest packed. Circles have many, many other issues with them. Hexagon only has 50% more sides than a square and could potentially net quite a few more chips from a die. Also the maximum variance in packaging trace length would go way down as well.0ldman79 - Thursday, October 11, 2018 - link
True, but you're talking die and he's talking package.Also they have a bit of dead space in the wafers and the die. It's not like there are transistors all the way to the edge of the chip.
Having multiple edges to avoid would probably actually cost them space vs a rectangle or square die.
willis936 - Thursday, October 11, 2018 - link
I was talking about both die and package. Hexagonal die would increase yields. Having both a hexagonal die and package would make package trace length shorter and have less variance between pins. A mathematic proof of this would be fun to do but it's easiest to convey the idea by imagining the worst case traces: the corners. The lower the outer angle of the corner, the shorter the trace has to be. A circle would be best where the outer corner angle is 180 degrees, but a hexagon's 240 degrees is much better than a rectangle's 270 degrees.I don't know if traces are the limiting factor in packaging size but it would help signal integrity at least.
thetuna - Thursday, October 11, 2018 - link
A hexagonal layout would make "dicing" the chips literally impossible :)woggs - Thursday, October 11, 2018 - link
Bingo.rahvin - Thursday, October 11, 2018 - link
So according to the wiki article on wafer dicing says that dicing other shapes is possible as long as they are using full cut laser which the article implies isn't as common as other methods. It doesn't say a hexgon is possible but if they are using computer controlled full depth laser cuts it would seem possible to get pretty much any shape.So accordingly rectangular dies aren't just because of dicing, there are lots of factors I'm sure that drive using rectangular dies. Things like simply history driving the tooling to all be geared towards rectangular dies because the early dicing techniques (physically cutting) were incapable of anything but straight lines all the way across the wafer. And simple things like the robotic picking and packaging is simpler with rectangular layouts.
I bet when you pile up all these reasons anything but rectangular just doesn't make sense.